In the realm of construction and excavation, the efficiency and durability of machinery like mini excavators hinge significantly on the health of their components, notably the mini excavator swing bearing. This pivotal part ensures the smooth rotation of the excavator’s arm and cabin, enabling precise movements and operations. However, like all mechanical components subjected to constant stress and environmental exposure, the swing bearing is prone to wear and degradation over time. Recognizing the signs that necessitate a mini excavator swing bearing replacement is crucial for maintaining operational efficiency and avoiding costly downtime.
The importance of timely swing bearing replacements cannot be overstated. The swing bearing is the heart of the excavator’s mobility. Neglecting its maintenance and timely replacement can lead to significant operational inefficiencies and safety risks.This sentiment is echoed across the industry, underscoring the need for regular inspections and proactive maintenance.
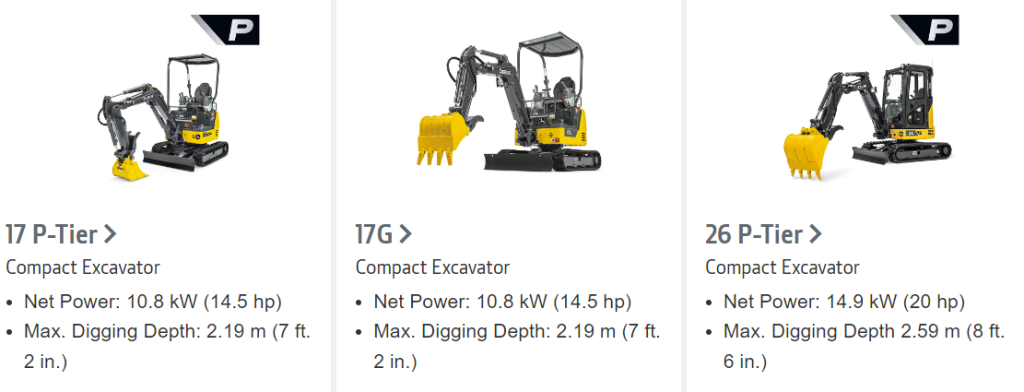
images source:https://www.deere.com/
This article delves into the critical aspects of mini excavator swing bearing replacement, offering insights into when and how replacements should be conducted, the signs of wear to watch for, and the steps involved in the replacement process. By integrating expert advice and focusing on key maintenance strategies, we aim to provide a comprehensive guide that supports the longevity and reliability of your mini excavator.
Understanding Mini Excavator Swing Bearings
The mini excavator swing bearing plays a pivotal role in the functionality and efficiency of mini excavators. This crucial component, located at the base of the excavator’s cab, allows for the smooth rotation of the cab and arm, enabling precise movement and operation in a variety of working conditions.
Application Fields
Mini excavator swing bearings find their applications in a broad spectrum of industries, including but not limited to, construction, mining, and engineering machinery. These bearings are essential for the operation of mobile and crawler cranes, highlighting their importance in the realm of heavy machinery and engineering equipment. The versatility and critical nature of swing bearings underscore their significance in ensuring operational efficiency and safety across various sectors.
Structural Features and Material Specifications
Swing bearings for mini excavators are designed with precision to withstand heavy loads while providing smooth rotational movement. They typically consist of an inner and outer ring, with rolling elements and seals. The materials used in their construction are selected for durability and resistance to wear and environmental elements, ensuring a long service life under rigorous operating conditions. The engineering behind these bearings focuses on reducing friction and handling both axial and radial loads efficiently.
Size Range and Model Compatibility
Swing bearings come in various sizes to accommodate the wide range of mini excavator models available on the market. From compact mini diggers ideal for small-scale projects to more robust excavators designed for mining operations, the swing bearing is a tailored fit to each model’s specifications. This customization ensures that each mini excavator swing mechanism operates at its peak, contributing to the machine’s overall performance and longevity.
The compatibility of swing bearings with different models is crucial for maintenance and replacement. Slewing Bearing Manufacturers often provide detailed guides on model interchangeability, aiding in the selection process for replacement bearings. This aspect is particularly important when considering mini excavator swing bearing replacement, as using the correct size and type of bearing is imperative for maintaining the excavator’s functionality and safety.
Understanding the fundamental aspects of mini excavator swing bearings—from their application in the field to the specifics of their structure and compatibility—is essential for operators and maintenance personnel. This knowledge not only facilitates efficient operation but also guides the maintenance and replacement processes, ensuring that mini excavators remain a reliable asset in various industrial applications.
Signs Your Mini Excavator Swing Bearing Needs Replacement
Identifying when a mini excavator swing bearing requires replacement is crucial for maintaining the efficiency and safety of your equipment. Recognizing the early signs of wear or damage can prevent more significant issues down the line, ensuring that your mini excavator remains operational and effective. Here are key indicators that it’s time to consider a mini excavator swing bearing replacement:
Identifying Wear and Tear
Wear Rate and Service Time: The lifespan of a swing bearing can vary based on usage intensity and maintenance practices. Regularly monitoring the wear rate and understanding the typical service time for your specific model can help predict when a replacement might be necessary.
Visible Damage: Inspecting the swing bearing for signs of physical damage, such as cracks, dents, or excessive wear, is vital. Visible damage often indicates that the bearing’s structural integrity is compromised, necessitating a replacement.
Symptoms of Failing Swing Bearings
Operational Inefficiency: Difficulty in swinging or a noticeable decrease in the smoothness of operation can signal that the swing bearing is failing.
Unusual Noises: Grinding, clicking, or popping sounds during operation are clear indicators of a problem within the swing mechanism, often pointing towards bearing issues.
Excessive Play or Movement: If the excavator’s upper structure exhibits more play or movement than usual, especially in the swing motion, it’s likely that the swing bearing is worn out.
Impact of Environmental Conditions
The operating environment can significantly affect the longevity of swing bearings. Operations in harsh conditions, such as extreme temperatures, dusty or muddy environments, and exposure to corrosive materials, can accelerate wear and shorten the bearing’s service life. Awareness of these conditions and their effects on your mini excavator swing components is essential for timely maintenance and replacement.
Expert Insight
According to Michael Richardson, a seasoned mechanic specializing in heavy machinery, “Regular inspection and maintenance are key to extending the life of your mini excavator’s swing bearing. However, once you notice significant wear or operational issues, delaying replacement can lead to more severe damage and higher repair costs.”
Recognizing the signs that your mini excavator swing bearing needs replacement is not just about maintaining operational efficiency; it’s also about ensuring the safety of the operator and the longevity of the machine. Timely replacement and proper maintenance can significantly reduce downtime and operational costs, keeping your mini excavator running smoothly for years to come.
Preparing for Swing Bearing Replacement
Before embarking on a mini excavator swing bearing replacement, proper preparation is crucial to ensure safety and efficiency throughout the process. Here’s how to set the stage for a successful bearing replacement:
Necessary Tools and Equipment
To replace a swing bearing, you’ll need a set of specific tools and equipment, including but not limited to:
A crane or hoist capable of lifting the excavator’s upper structure.
A comprehensive set of wrenches and sockets for removing bolts.
Bearing pullers or extractors for the removal of the old bearing.
A torque wrench for the precise installation of the new bearing.
Ensure all tools are in good working condition and are appropriate for the size and specifications of your mini excavator.
Safety Considerations and Preparatory Steps
Safety should be your top priority. Follow these steps to minimize risks:
Secure the Work Area: Make sure the excavator is on stable, level ground and that the work area is clear of unnecessary personnel and obstacles.
Support the Machine Properly: Use appropriate supports to safely hold the upper structure once it’s lifted off the undercarriage.
Disconnect the Battery: To prevent accidental starts, disconnect the excavator’s battery.
Step-by-Step Guide to Replacing Mini Excavator Swing Bearings
1.Disassembly for Access: Begin by removing any components that obstruct access to the swing bearing. This may include parts of the undercarriage, the drive motor, or even the excavator’s cab, depending on your model.
2.Removal of the Old Bearing: Once you’ve gained access to the swing bearing, carefully unbolt and remove it. This step requires caution and precision to avoid damaging surrounding components.
3.Installation of the New Bearing: Place the new swing bearing, ensuring it aligns correctly with the mounting points. Securely fasten it using the bolts, applying an even torque as specified by the manufacturer.
4.Lubrication: After installation, lubricate the new swing bearing according to the manufacturer’s guidelines. Proper lubrication is essential for the bearing’s performance and longevity.
5.Reassembly and Testing: Reassemble any removed components and reconnect the battery. Perform a comprehensive test to ensure the excavator operates smoothly and that the swing mechanism functions as expected.
Lubrication Practices Post-Installation
Proper lubrication after installation cannot be overstated. Use the recommended type and amount of lubricant, and follow the lubrication intervals specified by the manufacturer to prevent premature wear and ensure the swing bearing operates efficiently.
Expert Insight
John Peterson, an expert in construction equipment maintenance, emphasizes the importance of preparation: “Taking the time to properly prepare and having the right tools on hand can significantly streamline the mini excavator swing bearing replacement process, reducing downtime and ensuring the job is done correctly.”
Preparation is the foundation of a successful mini excavator swing bearing replacement. By following these guidelines and ensuring that all steps are meticulously planned and executed, you can enhance the safety and efficiency of the replacement process, ensuring your mini excavator returns to optimal operation with minimal disruption.
Maintenance Tips to Extend Swing Bearing Life
After successfully completing a mini excavator swing bearing replacement, implementing a robust maintenance routine is essential to extend the new bearing’s lifespan and ensure the continuous high performance of your mini excavator. Here are several maintenance tips to help you maximize the durability and efficiency of the swing bearing:
Regular Lubrication
One of the most critical aspects of swing bearing maintenance is regular lubrication. It reduces friction, minimizes wear, and protects against corrosion. Adhere to the manufacturer’s recommendations regarding the type of lubricant and the frequency of application. Proper lubrication ensures smooth operation and can significantly extend the bearing’s service life.
Frequent Inspections
Routine inspections can help catch early signs of wear or damage, allowing for timely interventions. Perform visual and manual checks regularly, looking for any signs of excessive wear, unusual noises, or movement within the swing mechanism. Early detection of potential issues can prevent more severe problems and costly repairs down the line.
Cleanliness
Keeping the swing bearing area clean is crucial for its longevity. Dirt, debris, and other contaminants can enter the bearing, causing abrasion and premature wear. Regular cleaning of the excavator, particularly after operation in dirty or dusty conditions, helps maintain the integrity of the swing bearing.
Operational Practices
How you operate your mini excavator can also impact the life of the swing bearing. Avoid pushing the machine beyond its designed capacity and operational limits, as excessive stress can accelerate wear on the swing bearing and other components. Being mindful of the excavator’s capabilities and adhering to best operational practices can help preserve the bearing’s condition.
Recognizing Early Warning Signs
Staying vigilant for early signs of swing bearing issues is crucial. Indicators such as difficulty in swinging, increased operational resistance, or unusual noises during rotation should prompt a more thorough inspection. Addressing these signs early can mitigate more significant problems and extend the bearing’s lifespan.
Expert Insight
Alex Thompson, a mechanical engineer with extensive experience in heavy equipment maintenance, advises, “Consistent maintenance is key to extending the life of your mini excavator’s swing bearing. A combination of regular lubrication, inspections, and adhering to proper operational practices can dramatically reduce the likelihood of premature failure.”
Conclusion
Effective maintenance of your mini excavator swing bearing post-replacement is vital for ensuring the longevity and reliability of your equipment. By following these maintenance tips and staying alert to the early warning signs of potential issues, you can maintain optimal performance and avoid the downtime and expense of unnecessary repairs. Remember, a well-maintained swing bearing is essential for the smooth and efficient operation of your mini excavator, making regular maintenance an investment in your equipment’s future.
Troubleshooting Common Swing Bearing Issues
Even with meticulous maintenance, swing bearings in mini excavators can encounter issues that affect their performance. Understanding how to troubleshoot common problems can help you quickly identify and address issues, minimizing downtime and repair costs. Here are strategies for diagnosing and resolving frequent swing bearing challenges:
Fault Diagnosis and Repair Techniques
Excessive Play or Movement: If the swing bearing exhibits excessive play, it’s often a sign of wear or internal damage. Inspect the bearing for any physical damage and check the tightness of the bolts. In some cases, adjustment or retightening may resolve the issue; otherwise, replacement might be necessary.
Unusual Noises During Operation: Grinding, clicking, or other abnormal sounds can indicate debris contamination or damage to the bearing’s rolling elements. Cleaning the area and inspecting the bearing for damage can help determine the next steps. Lubrication may reduce the noise, but persistent sounds likely indicate the need for replacement.
Difficulty Swinging: Resistance or difficulty in swinging the excavator’s arm could stem from lubrication issues or mechanical faults within the swing bearing. Ensure the bearing is adequately lubricated. If the problem persists, a more thorough inspection to check for damage or wear is warranted.
When to Seek Manufacturer Technical Support
Navigating complex issues or uncertainties regarding your mini excavator’s swing bearing may require expert advice. Manufacturer technical support can provide model-specific guidance, troubleshooting tips, and recommendations for repair or replacement. Leveraging this support ensures accurate diagnostics and appropriate solutions, safeguarding your equipment’s integrity.
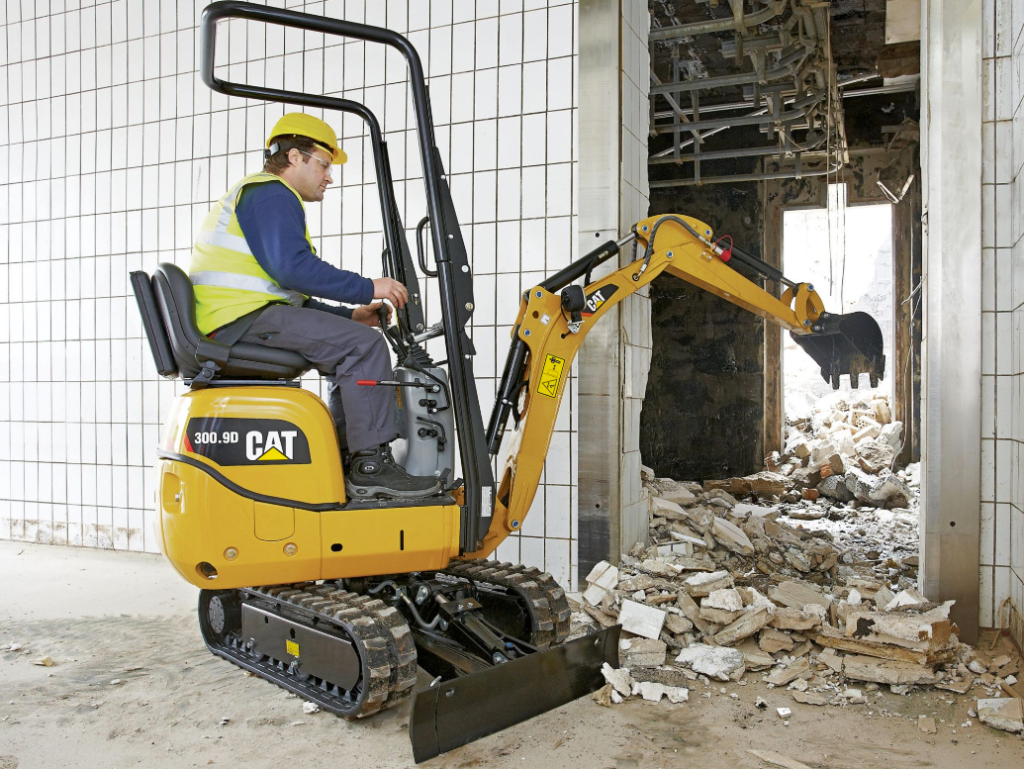
images source:https://www.cat.com/
Model Interchangeability and Sourcing Replacement Parts
Understanding model interchangeability is crucial when sourcing replacement parts for your swing bearing. Manufacturers often offer compatibility guides to assist in selecting the correct bearing for your specific mini excavator model. Opting for OEM (Original Equipment Manufacturer) parts guarantees compatibility and reliability, although aftermarket options can provide cost-effective alternatives without compromising quality.
Expert Insight
Emily Johnson, a field service technician specializing in mini excavators, emphasizes the importance of prompt action: “Addressing swing bearing issues at the first sign of trouble not only prevents further damage to your excavator but also maintains operational efficiency. Don’t hesitate to consult with experts or seek manufacturer support when faced with complex issues.”
Conclusion
Troubleshooting common mini excavator swing bearing problems is an essential skill for operators and maintenance personnel. By understanding how to diagnose and address issues such as excessive play, unusual noises, and operational difficulties, you can ensure the longevity and reliability of your excavator’s swing bearing. Always consider consulting with the manufacturer for technical support and ensure you select the correct model and quality parts for any replacements. Proactive troubleshooting and maintenance can significantly enhance your mini excavator’s performance and operational lifespan.
Selecting the Right Swing Bearing for Your Mini Excavator
When it’s time for a mini excavator swing bearing replacement, choosing the right bearing is crucial for ensuring optimal performance and longevity of your equipment. The market offers a plethora of options, making the selection process seem daunting. However, by focusing on a few key factors, you can make an informed decision that meets your excavator’s needs.
Factors to Consider
Load Capacity: Evaluate the maximum load your mini excavator handles. The swing bearing must be capable of supporting this load to prevent premature wear or failure.
Material Quality: High-quality materials are essential for durability and reliability. Bearings made from superior materials can withstand harsh conditions and offer longer service life.
Manufacturer Reputation: Opt for bearings from reputable manufacturers known for their commitment to quality and innovation. Brands like Caterpillar, Kubota, Bobcat, JCB, and Komatsu are renowned for their construction equipment parts, including swing bearings.
Compatibility: Ensure the swing bearing is compatible with your mini excavator model. Incorrect sizing or specifications can lead to operational issues and potential damage.
Comparison of Popular Brands and Models
Caterpillar Mini Excavator Swing Bearings: Known for their durability and precision engineering, Caterpillar’s swing
bearings are designed to meet the rigorous demands of construction work.
Kubota Mini Excavator Swing Bearings: Kubota bearings offer reliability and smooth operation, making them a popular choice among operators looking for efficiency and longevity.
Bobcat Excavator Mini Swing Bearings: Bobcat mini excavators are known for their reliability and performance across a wide range of construction and landscaping applications. The swing bearing, also known as the slewing ring or swing circle, is a crucial component that enables the excavator’s house to rotate smoothly on its undercarriage. It’s essential for precision work where the operator needs to maneuver the arm and bucket without moving the entire machine.
CAT Mini Slewing Ring Replacement | ||||
Excavator model number | Part number | Excavator model number | Part number | |
CAT 307 | 102-6377 | CAT 325C | 227-6087 | |
CAT 307C | 240-8361 | CAT 325 | 199-4483 | |
CAT 308C | 240-8362 | CAT 325 | 4178151 | |
CAT 312CL | 229-1077 | CAT 325 | 3530676 | |
CAT 311 | 231-6853 | CAT 325 | 2316854 | |
CAT 312B | 616411 | CAT 325CL | 199-4475 | |
CAT 312CL | 229-1077 | CAT 326 | 353-0649 | |
CAT 312C | 229-1077 | CAT 329D | 227-6087 | |
CAT 315 | 148-4568 | CAT 330 | 7Y0933 | |
CAT 318B | 148-4568 | CAT 330 | 1994559 | |
CAT M315 M318 | 145-4809 | CAT 330 | 353-0487 | |
CAT 315C | 229-1080 | CAT 330B | 231-6859 | |
CAT 319C | 227-6079 | CAT 330B | 114-1434 | |
CAT320B | 1141414 | CAT 330D | 227-6089 | |
CAT320BL | 121-8222 | CAT 330C | 227-6089 | |
CAT 320 | 7Y1565 | CAT330D/DL | 227-6090 | |
CAT 320B | 114-1505 | CAT 336D | 353-0489 | |
CAT 320BL | 177-7723 | CAT 336DL | 227-6089 | |
CAT 320BL | 114-1341 | CAT 336DL | 353-0680 | |
CAT 320C | 227-6081 | CAT 336D | 353-0490 | |
CAT 320C | 227-6147 | CAT 345 | 227-6052 | |
CAT 320C | 171-9425 | CAT 345B | 136-2969 | |
CAT 320D | 227-6082 | CAT 345B | 200-3645 | |
CAT 320L | 7Y1563 | CAT 345BII | 227-6094 | |
CAT 320L | 7Y1563 | CAT 345BL | 136-2970 | |
CAT 225 | 8K4127 | CAT 345BL | 169-5536/169-5537 | |
CAT 322C | 221-6764 | CAT 345DL | 227-6037 | |
CAT 324D | 227-6085 | CAT 345ECL | 227-6052 | |
CAT 325 | 7Y0745 | CAT 349D | 353-0490 | |
CAT 350 | 1026392 | CAT374 | 333-3009 | |
CAT 365C | 199-4565 | CAT374 | 367-8361 | |
CAT 365C | 227-6096 | CAT 385C | 199-4491 | |
CAT 365C | 227-6097 | CAT 385C | 227-6099 | |
CAT 365C | 199-4586 | CAT 385BL | 227-6098 | |
CAT 365CL | 267-6793 | CAT 385CL | 227-6099 | |
CAT 365CL | 397-9666 | CAT 390D | 227-6099 | |
CAT374F | 378-9586 |
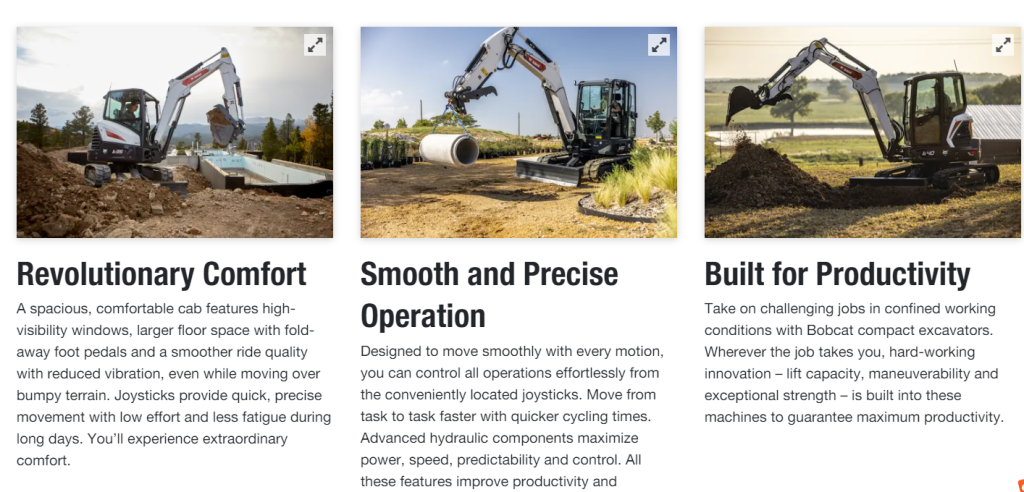
images source:https://www.bobcat.com/
Importance of Bobcat Mini Excavator Swing Bearings
Swing bearings in Bobcat mini excavators are designed to withstand the rigors of heavy use, offering both axial and radial support to the rotating upper structure. These bearings are critical for maintaining the excavator’s operational efficiency and safety. Over time, due to continuous use and exposure to environmental elements, the swing bearing may wear down or sustain damage, impacting the machine’s performance.
Maintenance and Replacement
Regular maintenance, including inspection and lubrication, is vital for extending the life of the swing bearing. Operators should regularly check for signs of wear, such as unusual noises, excessive play, or difficulty in swinging the excavator’s house. Early detection of issues can prevent more significant problems and costly downtime.
When it comes to replacement, using genuine Bobcat parts ensures compatibility and reliability. Bobcat swing bearings are engineered to meet the specific demands of their mini excavators, ensuring a perfect fit and optimal performance. It’s advisable to have a qualified technician perform the replacement to ensure the work is done correctly, following Bobcat’s specifications and guidelines.
JCB Mini Excavator Slewing Ring Replacement | |||
Excavator model number | Part number | Excavator model number | Part number |
JCB 8060 | 234/11000 | JCB JS220 | JRB0017 |
JCB 8085 | 831/10297 | JCB JS210 | JRB0017 |
JCB JS130 | 332/K8067 NEW | JCB 240 | JBB0001 |
JCB JS130 | JNB0146 OLD | JCB JS240 | 916/10029 |
JCB JS130 | JNB0160 | JCB 260 | 916/10029 |
JCB160 | 331/12091 | JCB 260 | JBB0001 |
JCB 205 | 333/P7280 | JCB JS330 | JSB0022 |
JS200LC | JRB0017 | JCB 360 | JSB0022 |
Excavator model number | Part number | Excavator model number | Part number |
PC15 | 20M-25-81201 | PC240-8 | 206-25-00301 |
PC18 | 20M-25-81201 | PC270 | 206-25-00400 |
PC75UU-2 | 201-25-61100 | PC290 | 206-25-00400 |
PC100-6 | 203-25-62100 | PC300 | 207-25-31112 |
PC110R | 206-25-11100 | PC300-3 | 207-25-00022 |
PC120-5 | 203-25-51200 | PC300-6 | 207-25-61100 |
PC120-6Z | 203-25-61100 | PC300-7 | 207-25-61100 |
PC120-6 | 203-25-62100 | PC300-7 | 207-25-61700 |
PC130-6 | 203-25-62100 | PC300LC-5 | 207-25-51100 |
PC130-7 | SAA4D95L | PC300LC-6 | 207-25-61100 |
A CASE excavator’s slewing ring is a critical component, pivotal for the machine’s functionality. The slewing ring, also known as a slewing bearing, enables the excavator’s upper structure to rotate smoothly over its undercarriage. It supports the weight of the upper structure while allowing it to turn 360 degrees without resistance. This part is crucial for excavators, including those from CASE, as it directly impacts the machine’s operational efficiency and precision.
Functionality and Importance
The slewing ring is made up of an inner and outer ring, with rolling elements (usually spherical or cylindrical rollers or balls) in between. These components are engineered to withstand axial, radial loads, and moment loads, making them essential for the heavy lifting and precise movements that excavators are known for. For a CASE excavator, the slewing ring is designed to meet the specific operational demands, including load-bearing capacity and rotation speed.
Maintenance and Replacement
Regular maintenance of the slewing ring is crucial for prolonging the life of a CASE excavator. Maintenance activities typically include regular inspections for wear and damage, ensuring proper lubrication, and checking for any abnormalities in movement or noise that could indicate an issue. Detecting problems early can prevent more significant issues and costly downtime.
The need for replacement of the slewing ring arises from wear and tear over time, which is inevitable given the demanding work environment of excavators. Signs that a slewing ring might need to be replaced include:
Difficulty in slewing (rotating) the excavator’s upper body
Excessive play or movement in the slewing ring
Unusual noises during operation, such as grinding or clicking
Visible signs of wear, such as uneven wear patterns or damaged rolling elements
Excavator model number | Part number | Excavator model number | Part number |
CASE CX130 | KNB10130 | CASE CX210B | KRB11710 |
CASE CX130 | KNB 0702 | CASE CX210C | KRB11710 |
CASE CX130 | KNB 0782 | CNH E215 | 72203516 |
CASE CX130 | KNB 0782 | CNH E215 | 87472588 |
CASE CX130 | KNB 10130 | CASE CX240 | KBB0878 |
CASE CX130 | KNB 11840 | CASE CX240 | KBB0282 |
CASE CX210 | KRB10190 | CASE CX240 | KBB 0759 |
CASE CX210 | KRB1347 | CASE CX240 | KBB 0898 |
CASE CX210 | KRB1603 | CASE CX240 | KBB 10080 |
CASE CX210 | KAR10150 | CASE CX240B | KBB11350 |
CASE CX210 | KBB1080 | CASE CX460 | KTB10010 |
CASE CX210 | KBB0759 | CASE 9030 | KRB10160 |
CASE CX210 | KRB10160 | CASE CX290 | KBB10100 |
CASE CX210B | KRB10160 | Case Cx460 | Ktb0847 |
CASE CX210 | KRB10180 |
Expert Insight
Mark Stevens, a product manager with over two decades in the construction equipment industry, advises, “Choosing the right swing bearing is about more than just fit; it’s about selecting a component that will enhance the performance and lifespan of your mini excavator. Always consider load requirements, material quality, and manufacturer reputation when making your selection.”
Conclusion
Selecting the right mini excavator swing bearing is a critical decision that impacts the performance, safety, and operational efficiency of your equipment. By considering factors such as load capacity, material quality, manufacturer reputation, and compatibility, you can ensure that your mini excavator continues to operate at its best. Always opt for reputable brands and models that align with your equipment’s specific needs, and don’t hesitate to consult with experts or manufacturers for guidance. Making an informed decision helps safeguard your investment and keeps your mini excavator running smoothly for years to come.
Conclusion: Ensuring Longevity and Efficiency with Proper Swing Bearing Maintenance
The mini excavator swing bearing replacement process is a critical maintenance task that directly impacts the longevity and efficiency of your mini excavator. From recognizing the early signs of wear and understanding the importance of selecting the right swing bearing, to conducting thorough maintenance and troubleshooting common issues, each step is vital in ensuring your equipment’s optimal performance.
Proper maintenance and timely replacement of the swing bearing not only prevent potential operational failures but also ensure the safety of operators and the reliability of the mini excavator over its lifespan. By adhering to the manufacturer’s guidelines for inspection, lubrication, and replacement, operators can significantly extend the life of their equipment, reduce downtime, and maintain high levels of operational efficiency.
Expert Insight
Experts in the field of construction machinery maintenance emphasize the importance of regular check-ups and maintenance routines. As Michael Richardson, a seasoned mechanic, notes, “The key to maximizing the lifespan and efficiency of your mini excavator lies in proactive maintenance and addressing issues promptly before they escalate.”
Final Thoughts
The maintenance of a mini excavator swing bearing is not just about ensuring the mechanical integrity of the equipment but also about safeguarding the investment made in purchasing this versatile machinery. With the right care, attention to detail, and adherence to recommended maintenance practices, operators can enjoy the full range of benefits that mini excavators offer to construction, mining, and engineering projects.
Choosing high-quality replacement bearings, staying vigilant for signs of wear, and committing to regular maintenance schedules are all crucial steps in maximizing the operational lifespan of your mini excavator. Remember, the swing bearing is at the heart of your mini excavator’s functionality; keeping it in top condition is essential for maintaining the productivity and efficiency of your construction operations.
Additional Resources
For operators and maintenance personnel looking to deepen their understanding of mini excavator swing bearing replacement and care, a wealth of resources is available. Expanding your knowledge through these materials can help ensure that your mini excavator remains a reliable and efficient part of your machinery fleet.
Where to Find OEM and Aftermarket Swing Bearings
OEM Parts Suppliers: Most excavator manufacturers offer their own parts supply services, providing access to original equipment manufacturer (OEM) swing bearings that guarantee compatibility and reliability.
Aftermarket Suppliers: Reputable aftermarket brands also offer high-quality swing bearings often at a lower cost, providing a viable alternative to OEM parts. Ensure that the aftermarket supplier has a solid reputation for quality and service.
Online Forums and Communities for Mini Excavator Enthusiasts and Professionals
Construction Machinery Forums: Online communities and forums are excellent places to share experiences, get advice, and find recommendations on parts suppliers and maintenance tips.
Social Media Groups: Platforms like Facebook and LinkedIn host groups dedicated to construction equipment, where members discuss maintenance issues, including mini excavator swing bearing replacement.
Professional Development and Training
Manufacturer Training Programs: Many manufacturers offer training programs for operators and technicians, covering everything from routine maintenance to complex repairs.
Vocational Schools and Community Colleges: These institutions often provide courses in heavy equipment operation and maintenance, offering hands-on experience and theoretical knowledge.
Technical Manuals and Guides
Service Manuals: The manufacturer’s service manual is an invaluable resource, offering detailed guidance on every aspect of mini excavator maintenance, including swing bearing replacement.
Online Tutorials and Videos: Platforms like YouTube feature numerous tutorials from experienced mechanics and operators, providing step-by-step guides on various maintenance tasks.
By leveraging these resources, you can gain a more profound understanding of the intricacies of mini excavator swing bearing maintenance and replacement. This knowledge not only aids in performing effective maintenance and replacements but also helps in making informed decisions regarding parts selection and maintenance strategies. Ultimately, investing time in learning and staying informed is key to maximizing the performance and lifespan of your mini excavator.
Thank you for following along with this comprehensive guide on Mini Excavator Swing Bearing Replacement. Through understanding the importance of this crucial component, recognizing signs of wear, preparing for replacement, and committing to regular maintenance, you can ensure the longevity and efficiency of your mini excavator. This guide has covered everything from the basics of swing bearings, through the detailed process of replacement, to post-replacement care and troubleshooting common issues. We’ve also highlighted the importance of selecting the right swing bearing and where to find further resources for continued learning and support.
Remember, the key to maximizing the operational lifespan and efficiency of your mini excavator lies in proactive maintenance and addressing issues before they escalate. Regular checks, proper lubrication, and adhering to operational best practices are paramount. Utilize available resources, from OEM and aftermarket suppliers to online forums and professional training, to stay informed and skilled in managing your equipment’s needs.
The world of construction machinery is ever-evolving, with new technologies and methodologies emerging. Staying abreast of these developments, especially in critical maintenance areas like swing bearing replacement, ensures that your operations remain productive, safe, and cost-effective.
We hope this guide serves as a valuable resource in your maintenance practices, helping you to maintain the health and efficiency of your mini excavators for years to come. For further information, don’t hesitate to consult with manufacturer resources or seek advice from industry professionals. Your diligence and commitment to maintenance excellence are what will keep your machinery—and your projects—moving forward.
FAQ:
How Do You Check a Swing Bearing on an Excavator?
Inspecting the swing bearing of a mini excavator is a critical maintenance task that ensures the longevity and optimal performance of the equipment. The mini excavator swing bearing is the pivotal component that allows the cab and the attachment arm to rotate smoothly. Given its importance, regular checks are essential to prevent operational downtime and costly repairs. Here’s an authoritative guide on how to conduct these inspections effectively, incorporating a wide range of mini excavators, including popular models like the Kubota mini excavator, Caterpillar mini excavator, and Komatsu mini excavator.
Initial Visual Inspection
Start with a comprehensive visual inspection of the mini excavator swing bearing. Look for signs of external wear, such as cracks, corrosion, or any deformation. These visual cues can be early indicators of internal damage or failure. It’s crucial to assess the integrity of the swing bearing, especially if the mini excavator is a heavily used piece of machinery or if you’re considering a mini excavator for sale or rent.
Auditory Checks
Operate the mini excavator and listen carefully to the sounds emanating from the swing mechanism. Any abnormal noises, such as grinding, clicking, or squealing, can indicate that the bearing is experiencing undue stress or friction. These auditory signs should not be ignored, as they can lead to a mini excavator swing bearing replacement if left unaddressed.
Manual Testing for Play and Movement
Another essential step is to manually test the swing bearing for excessive play or movement. With the machine turned off and in a secure position, attempt to move the cab side to side and observe any unusual movement. A healthy swing bearing will have minimal play, ensuring that the excavator’s cab and arm can rotate accurately and efficiently.
Checking Lubrication Levels
Proper lubrication is paramount for the swing bearing’s operation. Check the lubrication levels and the condition of the lubricant. Contaminated or insufficient lubricant can cause increased wear and tear, significantly impacting the mini excavator swing mechanism’s lifespan and performance. Ensure that the lubrication practices align with the manufacturer’s specifications for your specific model, be it a Kubota mini excavator, Caterpillar mini excavator, or any other brand.
Consult Manufacturer’s Guidelines
Each brand, whether it’s a Bobcat excavator mini, Deere mini excavator, or JCB mini excavator, may have specific recommendations for checking and maintaining the swing bearing. It’s imperative to consult the manufacturer’s guidelines to understand the specific needs of your machinery. This is especially true for owners of specialized models like mini dozers or those looking for a mini digger for sale.
When to Consider Replacement
Should you discover any issues during your inspection, considering a mini excavator swing bearing replacement might be necessary. It’s a significant maintenance task that can restore the operational integrity and efficiency of your mini excavator. Remember, the cost of a mini excavator price reflects not just the initial purchase but also the ongoing maintenance and potential replacement parts like swing bearings.
Conclusion
Regular inspections of the mini excavator swing bearing are crucial for maintaining the equipment’s functionality and safety. By incorporating visual checks, auditory monitoring, manual testing, and proper lubrication assessments into your maintenance routine, you can significantly extend the life of your mini excavator. Always adhere to the manufacturer’s recommendations for specific models, whether it’s a Kubota mini excavator, Caterpillar mini excavator, or Komatsu mini excavator, to ensure precise maintenance and, when necessary, accurate replacement. This proactive approach to maintenance is key to maximizing the investment in your mini excavator fleet.